RESEARCH
Nowadays the robotic research focuses on building systems that can effectively and safely interact with the environment. In the near future, robotic systems will not only be used in the familiar areas but also be used to collaborate with humans and even worn by the humans to perform more complicated tasks in various applications. However, the physical and functional properties of the robots are limited by their actuator, sensor components and by their physical architecture. We need to find new methodologies for building soft structures, embedded/wearable sensors and actuators that enable more functions. In Flexible Systems Laboratory we use smart materials, biologically inspired design, layer-by-layer fabrication techniques, and try to find solutions to make architectures soft, flexible, embeddable and wearable.
Projects: Our projects have been supported by TUBITAK.
Wearable Lower Body Exoskeleton System with Flexible Clothing
In this project, a novel wearable exoskeleton with flexible clothing will be developed for the use of paraplegic persons who have lost their lower extremity motor functions due to low back pain, paralysis and similar disturbances. This prototype will be designed as a rigid-link exoskeleton that is actuated via series-elastic actuators. The user’s physical state will be observed using soft elements attached to a wearable sensorized clothing, which will be used in conjunction with the exoskeleton. This project is supported by Tubitak 1003 (Grant no: 118E924). (Uğurlu B. et al. ICORR 2019)
Design and Manufacturing of Novel Systems for Miniature Parallel Robots
The goal of this project is to design and manufacture miniature, scalable, portable parallel robots with closed loop feedback control algorithm using embedded position sensors. This project aims to build new generation robotic systems which are novel, national, commercializable, low-cost, scalable, adaptable and providing high precision micro positioning. This project is supported by Tubitak 1003 (Grant no: 216M193). (Acer Kalafat M., Sevinç H., Samankan S., Altınkaynak A. & Temel Z., J. Mechanisms Robotics, 2021)

Tactile System Design for Texture Recognition and Realization
The purpose of this project is to design, manufacture and cooperate the tactile sensor and the tactile actuator. In this project, a piezoelectric (PZT) based, having 3x3 matrix form, flexible, low profile tactile sensor and a tactile actuator having 9 magnetic pins have been developed. The mechatronic integration of the designs has been achieved and a new tactile system has been established. The references for controlling the tactile actuator have been provided by sensing the force localization and surface geometries with the tactile sensor. This project is supported by Tubitak 3501 (Grant no: 215E139).
(Acer M.& Yıldız F. WeRob 2018, Acer M.,Yıldız F.&Bazzaz H., ICAT 2017)
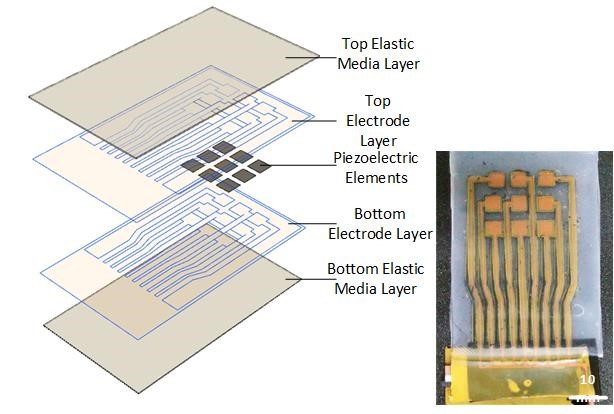
Optimization of Manufacturing Parameters of 3D FDM Printers
In this project, the performance characteristics of three different plastic material (ABS, PET, and PLA) is investigated. For this purpose, first, a numerical model of the extruder head region where the plastic melting occurs is established. From the numerical model, the dimensional tolerances for different extruder head temperatures and feed rates is obtained and these values is compared with the ones obtained from the experiments. According to the numerical and experimental results, the numerical model is updated. Thus, a tool that will give the proper dimensional tolerances at an extruder head temperature and feed rate for a specific plastic is obtained. Later, developed numerical model is used to obtain the optimum extruder head diameter and length that gives similar dimensional tolerances for faster manufacturing times. This project is supported by Tubitak 3501. (Hıra O, Yücedag S, Samankan S., :Çiçek ÖY, Altınkaynak A., Progress in Add. Man.).